特注バット溶接機
お客様のご要望に100%合致した、
最適なバット溶接機を提供します
バット溶接機 ソリューションナビを運営する東京新電機では、
お客様のご要望に合致した特注機の設計・開発を通じて、皆様の困難な課題を解決いたします。
こんなご要望にお応えします!
- 鉄以外の材質のワークを接合したい…
- 異材接合を行いたい…
- 単純形状ではないワークを接合したい…
- 極小のワークを接合したい…
- バット溶接工程を自動化したい…
- 溶接強度を向上させたい…
- 溶接品の直角度、平面度、同軸度等の精度を上げたい…
- 限られた有効スペースに機械を収めたい…
特注バット溶接機 設計開発サービスの特徴
POINT1 特注バット溶接機の設計・開発実績は400件以上 (2023年時点)!汎用機では対応できない、多様なニーズにお応えします
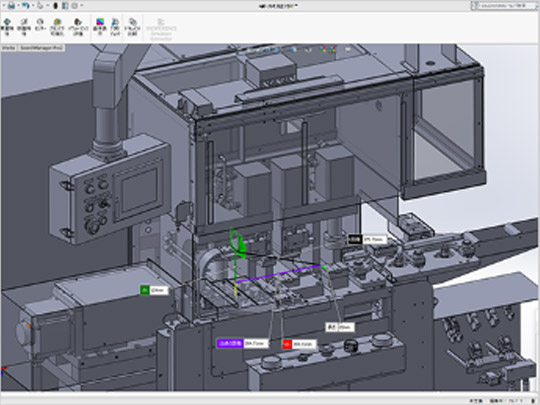
当社は、特注バット溶接機の豊富な設計・開発実績を持ち、お客様の課題解決のパートナーとして活動してきました。
お客様のご要望に合致した特注バット溶接機の開発実績は400件以上(2023年時点)であり、電極仕様・トランス仕様・クランプ機構をはじめとした項目で多様なニーズに対応しています。
「既存のバット溶接機では生産性が上がらない…」
「他社製バット溶接機では汎用品しかなく、いくつかの要素を妥協しないといけない…」
とお悩みの皆様、お気軽に当社にご相談ください。
主なカスタマイズ項目
- 電極仕様
- トランス仕様
- クランプ機構
- 装置サイズ
- ワーク流れ方向
- ワーク供給仕様(自動化等)
- 製品組み込み型へのカスタマイズ 等
POINT2 自動化にも対応します!自動バット溶接ラインの構築により、生産性の大幅向上を実現します!
当社は、創業以来、バット溶接機だけでなく産業用自動機の開発にも力を入れてきました。自動化ノウハウとバット溶接ノウハウを融合して、自動バット溶接機の開発を行っています。
バット溶接機をすでにご使用中の皆様、自動化により大幅な生産性向上を実現できる可能性があります。まずはご要望をお聞かせください。最適な提案を行うことをお約束します。
POINT3 製作台数は1台から!材質・ワーク形状・ワークサイズなど、ご要望に合致した特注機を設計・開発します!
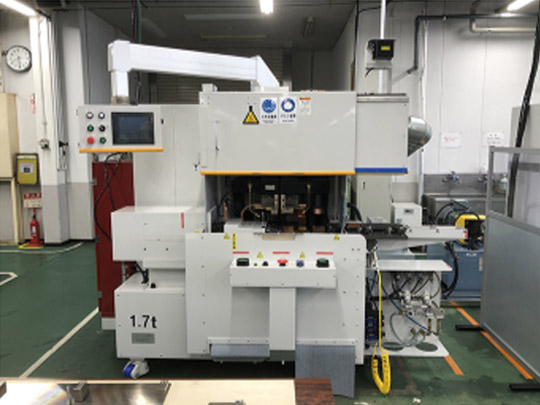
海外メーカーをはじめ、バット溶接機メーカーは多々ありますが、特注対応を行うメーカーは多くありません。その理由は、「製作台数」にあります。特注機は設計・製作工数がかかり、量産化されないことが多いため、利益率が低下しやすいという課題があり、他社が嫌がる領域です。
当社は、特注バット溶接機の開発ノウハウを持ち、「無理難題に対応できる企業」として多くのお客様に選ばれています。
製作台数は1台からお受けします。
他社に断られた無理難題を当社にご相談ください。特注バット溶接機にて課題を解決します。
特注バット溶接機の開発事例
当社は特注バット溶接機の開発実績を多く保有します
バット溶接機ソリューションナビを運営する東京新電機は、特注機・カスタマイズ機の開発を強みとしており、課題解決のパートナーとして選ばれています。当社の特注バット溶接機の開発実績をご紹介します。
軸受け用特殊鋼帯鋼用 特注バット溶接機
特注機の開発により、段取り替え時間50%低減、溶接リードタイムの大幅短縮を実現した開発事例です。
従来はTIG溶接にて接合を行っており、ワーク変更に伴う段取り替え作業を5分×10回以上、1日に実施しており、トータルで非常に多くの時間がかかり非効率な生産が行われていました。TIG溶接の接合はそもそも溶接に時間がかかり、さらに溶接技術が必要であり対応できる人材が少ないという課題もあり、当社にご相談頂きました。
お客様のご要望に合致した標準機はなく、特注機にてご提案させて頂きました。導入後、溶接時間は5秒以下を実現、段取り替え時間は50%低減することが出来ました。
大口径メタルパッキン用 特注バット溶接機
特注機の開発により、材料コストの低減と溶接品質の向上を実現した事例です。
先の事例と同様に、従来はレーザカット、TIG溶接にて製造をしていましたが、廃棄する材料が多いため歩留まりが悪く、材料コスト低減が課題となっていました。また、溶接部の強度不足でくぼみ・ボイド・巣等の欠陥が生じやすくなってしまう課題もあり、バット溶接への工法変換をご検討されました。
お客様要望に合致したフラッシュバット溶接機の導入により、材料無駄をゼロにし、さらに高強度溶接の実現、不良率0%の生産が可能になりました。
耐火物用鉄枠用 特注バット溶接機
特注機の開発により、生産タクト短縮、溶接強度向上、ランニングコストの低減を実現した事例です。従来はCO2溶接にて角材の接合をされていましたが、1本あたり10秒以上の加工時間がかかり溶接時間が非常に長く、2台のロボットで並行して溶接を行うため広いスペースも必要で、工場を圧迫しているとのことでした。さらに、溶接に伴う消耗品のランニングコストが上昇しており、低減を課題とされていました。
お客様要望に合致したフラッシュバット溶接機を提案させて頂き、接合テストも問題なくクリアできたため、導入が決定しました。結果、従来1本あたり10秒以上かかっていた溶接時間も、5秒以下と半分以下に短縮することができ、設置スペースも省略できたとお喜び頂きました。